In applications awesome heat materials that contain industrial and manufacturing processes, heat platen coated with PTFE is a necessity. It is characterized by non-stick features and high abrasion resistance and is widely employed in textile paint, graphic arts, food-processing, electrical and electronics industries and other uses. In this guide, the author further explores what is a PTFE coated heat platens are, how they are used, the benefits of the heat platen, and how best to maintain the heat platen.
Understanding Heat Platens
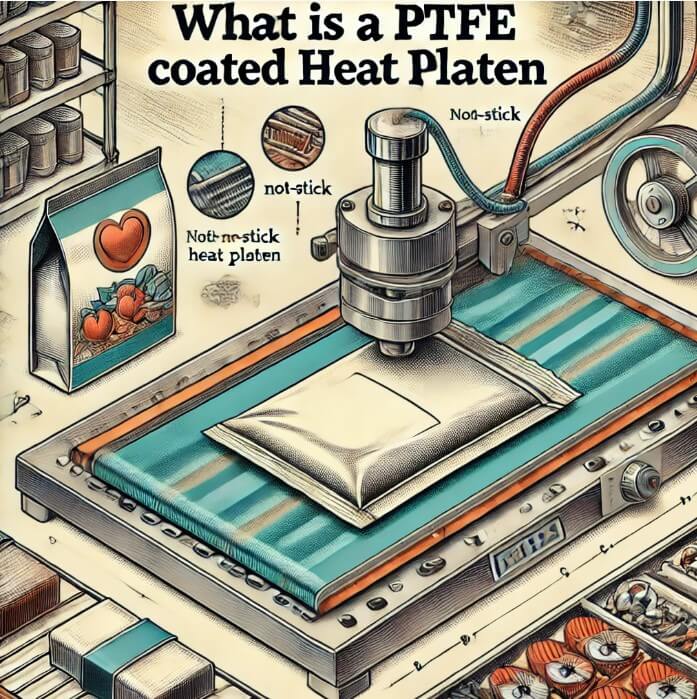
Heat platen is a flat metal surface with heating element that is usually used to apply heat and pressure to objects during heat transfer printing, lamination and sealing. It has a special function in guaranteeing that the heat is spread uniformly over a substrate or material. PTFE coating of the platen improves the efficiency and precision of these devices.
What is PTFE?
PTFE is an artificial fluoropolymer that is special in its kind. Commonly recognized by its brand name Teflon, PTFE is widely used in various industrial applications due to its:
Non-stick Surface: Reduces the chances of formation of deposits on the surface of the treated article.
High Heat Resistance: Is not affected by high or low temperatures.
Chemical Resistance: It is rather resistant to most chemicals, making it built to last.
Low Friction: Causes for proper slippage between the subsequent surface.
PTFE coated heat platen: Detailed characteristics
Non-Stick Surface: Reduces the chance of adhesives, inks, or other materials to adhere to a surface.
Even Heat Distribution: Ensures equal heating of the distinguished part on the surface.
Durability: It has a high durability, has an antimetallic layer to avoid scratches and is highly resistant to chemical abrasion.
Ease of Cleaning: Dirt and grime can be cleaned out by wiping conveniently.
High Temperature Tolerance: Is capable of working at high temperature ranges as produced by hot fluids and gases.
Uses of PTFE-Coated Heat Platens
PTFE-coated heat platens are versatile and find applications in numerous industries, including:
1. Textile Printing and Heat Transfers
As one of its subsectors, the Textile Printing and Heat Transfers has been influenced by these changes. Vital when using sublimation printing for clear and bright prints on fabrics. In heat transfer vinyl (HTV) for garment embellishment.
2. Industrial Sealing
Used in machines involving the sealing of food stuffs packaging. Forms incredibly leak-proof and watertight joints without adhering to the substrate.
3. Laminating Processes
The ideal laminating machine for laminating laminating wood, paper, plastic and other substances. It seals to allow even laminating and can never leave bubbles on the laminated item.
4. Composite Forming
Used widely in car manufacturing industries and aircraft industries as a means of forming and molding composites.
It is crucial to discuss the positives associated with a PTFE coated heat platen to appreciate its importance to the users in this section.
The PTFE coating adds multiple benefits to traditional heat platens:
Efficiency: Saves time by avoiding time consuming removal of residue on the tools.
Cost-Effective: Extends the service life of the platen thus lowering on the money needed to effect a replacement.
Versatility: Universal type suitable for most applications and all materials.
Improved Quality: Readily ensures an even distribution of the conducted or performed processes in various substrates.
Reduced Maintenance: Maintenance is low because they easily repel dirt and can be wiped with a cloth with no difficulty.
Regular Heat Platens vs. PTFE-Coated Heat Platens
Feature | Regular Heat Platen | PTFE-Coated Heat Platen |
---|---|---|
Non-stick Surface | No | Yes |
Heat Resistance | Moderate | High |
Ease of Cleaning | Difficult | Easy |
Durability | Lower | High |
Applications | Limited | Versatile |
PTFE-Coated Heat Platens: Helpful Information for Proper Usage
Clean Regularly: After each use wash the hair with warm water and wipe off any excess residue with a clean, soft and damp cloth.
Avoid Abrasives: Avoid the point interesting tools or hardness cleaning materials.
Inspect Periodically: Grilles may exhibit signs of wear or damage to the PTFE and can easily be identified by their structure.
Follow Temperature Guidelines: Restrict operation work above the recommendations standard temperature limits.
Frequently Asked Questions about PTFE coated heat platens
1. What is a PTFE coated heat platen?
PTFE coated heat platen is a heat transfer surface covered with fluoro-carbon polymer poly tetra fluoro ethylene. It find application in industrial processes such as heat exchanging, lamination, and sealing.
2. What are the strengths of PTFE coating?
It has non stick properties, high heat resistance, and high use durability which is why PTFE coated products fit almost any environment.
3. Can anyone offer information on how a PTFE-coated heat platen should be cleaned?
All you need to do is damp a piece of cloth and gently wipe the surface. Do not use abrasives when cleaning or when working on your surfaces.
4. What are the production fields of PTFE coated heat platens?
Some of the applications include textile printing, packaging, food processing and forming of composites.
5. Is it possible to repair a damaged PTFE coating?
Indeed, the PTFE layer may be recoated in many instances where it has become worn out or eroded.
Conclusion
The PTFE coated heat platen is indispensable in industries where heat application is central and the performance has to be optimum. Its non stick surface hence it does not require the use of any external cover and its durability and versatility make it quite ideal for such processes as textile printing, sealing and laminating. In learning all the particulars of operant chamber, it is possible to maximize its benefits and guarantee the long-term use as well as task completion standards.
Read more on Thinkow.